基于Fluent的徑向滑動(dòng)軸承油膜特性的仿真分析
2017年07月19日
1. 引言
長(zhǎng)期以來(lái),利用求解雷諾方程的方法研究滑動(dòng)軸承特性具有計(jì)算時(shí)間短的突出優(yōu)點(diǎn),然其求解過(guò)程中忽略了慣性項(xiàng)、油膜曲率等因素的影響。近年來(lái),隨著計(jì)算流體力學(xué)技術(shù)的發(fā)展和計(jì)算機(jī)性能的提高,在實(shí)驗(yàn)的基礎(chǔ)上通過(guò)CFD建模分析的方法,可以更好地對(duì)油膜軸承動(dòng)特性進(jìn)行描述,完成實(shí)驗(yàn)難以實(shí)現(xiàn)的力場(chǎng)測(cè)試。本文以公司DQ11-100電機(jī)滑動(dòng)軸承為原型,通過(guò)Proe創(chuàng)建油膜三維模型并利用Gambit劃分網(wǎng)格建立有限元計(jì)算模型,利用CFD軟件Fluent對(duì)動(dòng)壓徑向軸承在穩(wěn)態(tài)下的三維力場(chǎng)進(jìn)行仿真分析。
2. 計(jì)算模型及網(wǎng)格劃分
2.1 軸承物理模型的尺寸
軸承簡(jiǎn)化物理模型如圖1所示,采用頂端供油,主軸順時(shí)針轉(zhuǎn)動(dòng)。
軸瓦內(nèi)孔直徑D=100mm;軸瓦寬徑比B/D=1;依照生產(chǎn)經(jīng)驗(yàn)及相關(guān)公式,直徑間隙h=0.2013mm,據(jù)滑動(dòng)軸承流體動(dòng)壓潤(rùn)滑理論,解得偏心率ε=0.6013,油膜偏位角θ=49.95°。
其他參數(shù):初定電機(jī)轉(zhuǎn)速n=3000r/min;潤(rùn)滑油密度設(shè)定為895Kg/m3,同時(shí)據(jù)經(jīng)驗(yàn)公式,潤(rùn)滑油動(dòng)力粘度0.018Pa·s;考慮潤(rùn)滑油粘性生成熱,取定潤(rùn)滑油比熱容為1885J/(Kg·K),熱傳導(dǎo)系數(shù)為0.4W/(m·K)。
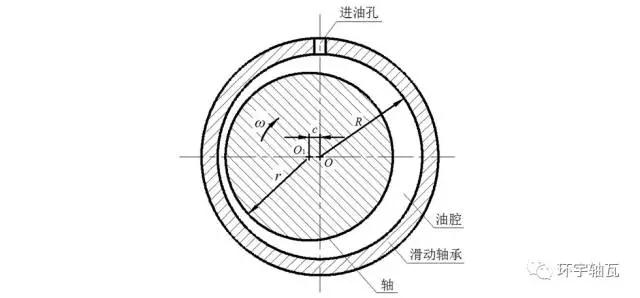
圖1 滑動(dòng)軸承軸向結(jié)構(gòu)示意圖
2.2 Fluent計(jì)算模型及網(wǎng)格劃分
據(jù)上相關(guān)尺寸參數(shù),于Proe中繪制滑動(dòng)軸承油膜計(jì)算模型,考慮到軸承以及油膜潤(rùn)滑的對(duì)稱(chēng)性,為縮減計(jì)算時(shí)間,模型僅繪制一半,如圖2a所示。
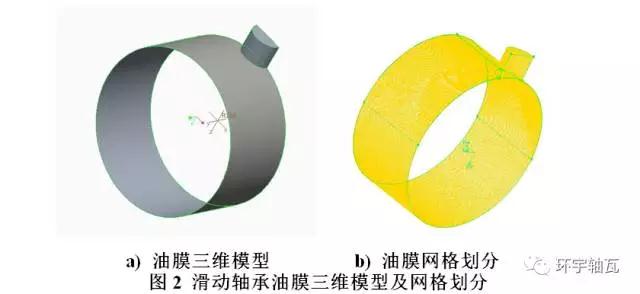
而后利用Gambit軟件進(jìn)行網(wǎng)格劃分,為保證精度及后續(xù)求解計(jì)算的收斂,采用結(jié)構(gòu)化網(wǎng)格,油膜厚度方向劃分三層且等距分布,適當(dāng)增加網(wǎng)格密度并作對(duì)稱(chēng)面處理,如圖2b所示。
3. Fluent模擬仿真
3.1 多相流油膜計(jì)算條件的設(shè)置
模型的設(shè)定:采用壓力基隱式求解器,三維的層流穩(wěn)態(tài)模型,多相流模型使用混合模型Mixture,相數(shù)為兩相。開(kāi)啟能量方程,在能量方程中包含粘性生成熱ViscousHeating。
物相的設(shè)定:第一相為潤(rùn)滑油oil,其有效密度為895kg /m3,有效動(dòng)力粘度為0.018Pa·s,比熱容為1885J/(Kg·K),熱傳導(dǎo)系數(shù)為0.4W/(m·K)。第二相為空氣air,其物性參數(shù)取自Fluent自帶數(shù)據(jù)庫(kù)。
邊界條件的設(shè)定:選混合物為計(jì)算流體。進(jìn)口壓力設(shè)定為2000Pa,出口壓力默認(rèn),設(shè)定主軸轉(zhuǎn)速3000r/min,轉(zhuǎn)速定義到油膜的壁面上。啟用空穴模型,空氣的初始體積分?jǐn)?shù)0.1,油膜破裂壓力為7550Pa,即當(dāng)油膜壓力低于7550Pa時(shí),將析出空氣。
3.2 計(jì)算結(jié)果
圖3分別為偏心率ε=0.6013,轉(zhuǎn)速n=3000r/min時(shí)的多相流油膜壓力場(chǎng)、密度場(chǎng)、能量場(chǎng)以及溫度場(chǎng)(開(kāi)氏溫度)分布。可見(jiàn),
1) 油液從頂端進(jìn)油孔流入,從軸瓦兩端流出。油膜分布在最小油膜厚度附近呈現(xiàn)非常明顯的壓力集中區(qū),順著轉(zhuǎn)軸旋轉(zhuǎn)方向,壓力從進(jìn)油口逐漸增大達(dá)到正壓峰值后減小,通過(guò)最小油膜厚度處后進(jìn)入發(fā)散區(qū),同時(shí)混合相密度逐漸減小,油膜在負(fù)壓區(qū)迅速破裂,從而進(jìn)一步影響了油膜的壓力分布;
2) 在正壓區(qū),油膜溫度較低,溫升順著潤(rùn)滑油流動(dòng)方向從低溫區(qū)向軸承兩端擴(kuò)張,同時(shí)隨著軸頸轉(zhuǎn)動(dòng)方向,溫度逐漸遞增,且在油膜上半部分的負(fù)壓區(qū)條帶狀區(qū)域內(nèi)達(dá)到溫升極限,繼而由于低溫潤(rùn)滑油從進(jìn)油口的遞補(bǔ),溫升又逐漸降低。
因而,通過(guò)壓力分布和溫度分布圖可有針對(duì)性地改進(jìn)軸承的散熱結(jié)構(gòu),為軸承設(shè)計(jì)提供重要的理論依據(jù),大大降低多次實(shí)驗(yàn)所需的高額成本。
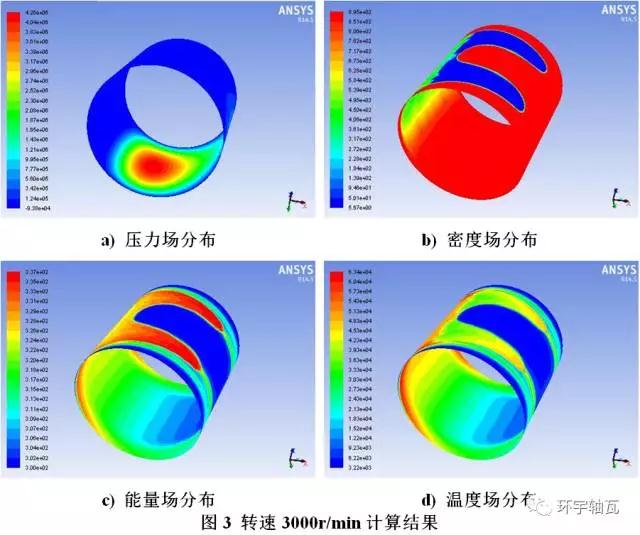
3.3 主軸轉(zhuǎn)速對(duì)油膜特性的影響
改變主軸轉(zhuǎn)速進(jìn)行多次仿真計(jì)算,得到收斂后的穩(wěn)態(tài)徑向滑動(dòng)軸承在轉(zhuǎn)速分別為1000r/min、1500r/min、2000r/min、6000r/min時(shí)的壓力場(chǎng)分布和溫度場(chǎng)分布分別如圖4、圖5所示。
隨著轉(zhuǎn)速增大,油膜壓力增大,油膜壓力分布形態(tài)大致相同,周向油膜承載角度逐漸向最小膜厚位置方向收斂;且轉(zhuǎn)速越大,溫升越高,溫升集中區(qū)越明顯,軸向溫度等值線(xiàn)向軸承中心位置收斂。
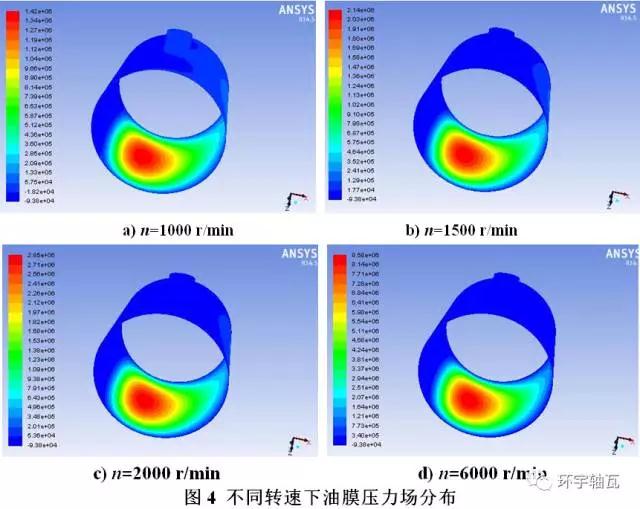
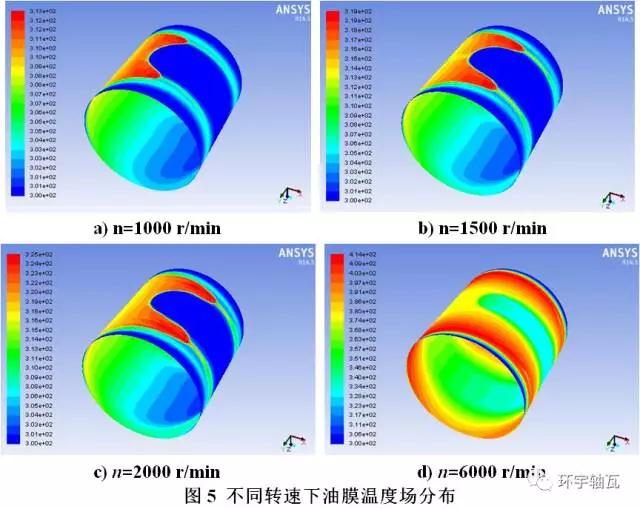
不同轉(zhuǎn)速仿真實(shí)驗(yàn)中,軸瓦內(nèi)孔100mm、寬徑比為1,潤(rùn)滑油入口油溫27℃,偏心率、直徑間隙等參數(shù)為定值,設(shè)定不同的主軸轉(zhuǎn)速,其計(jì)算結(jié)果數(shù)據(jù)如表1所示。據(jù)此可知,隨著主軸轉(zhuǎn)速增加,油膜壓力極值及增大,溫度極值及溫升均顯著升高,偏位角逐漸變小,軸心有下移趨勢(shì),油膜承載能力也隨之增強(qiáng)。顯然,主軸轉(zhuǎn)速對(duì)油膜特性的影響規(guī)律與經(jīng)典軸承理論相吻合。
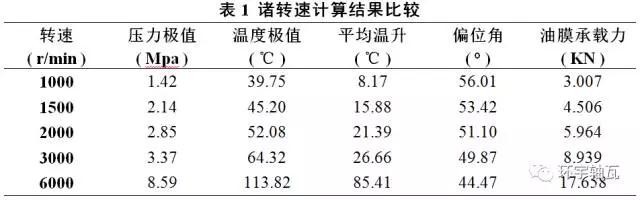
3.4 軸承參數(shù)的優(yōu)化計(jì)算
如表1所示,轉(zhuǎn)速為6000r/min時(shí),壓力極值極大,溫度極值和溫升已超出巴氏合金軸瓦的工作溫度,因而此組條件參數(shù)不再適用。
重新計(jì)算軸瓦直徑間隙和潤(rùn)滑油粘度,并進(jìn)行油膜特性仿真實(shí)驗(yàn),壓力場(chǎng)分布及溫度場(chǎng)分布如圖6所示。具體仿真數(shù)據(jù)結(jié)果如表2所示,可見(jiàn),壓力極值和溫度極值已大幅降低,理論上已滿(mǎn)足實(shí)際使用條件。
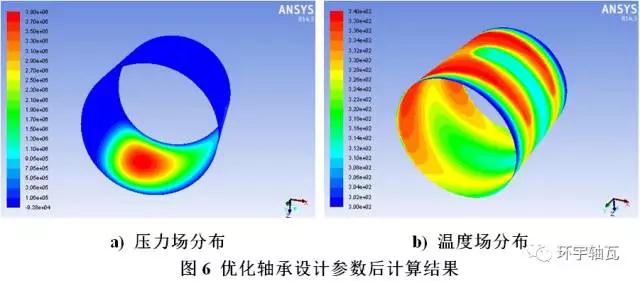
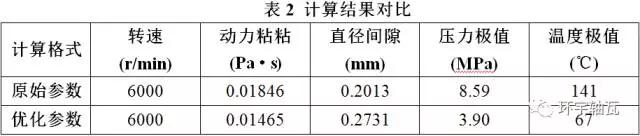
4. 結(jié)論
建立了基于Fluent的滑動(dòng)軸承油膜計(jì)算分析模型,引入空穴模型以及粘溫特性,給出流體流動(dòng)壓力場(chǎng)、溫度場(chǎng)的時(shí)變分布情況,較為準(zhǔn)確地反映滑動(dòng)軸承軸承油膜穩(wěn)態(tài)特性,預(yù)測(cè)流體在軸承中的流動(dòng)狀態(tài)和油膜的整體性能。工程設(shè)計(jì)與優(yōu)化對(duì)實(shí)驗(yàn)的依賴(lài)性將大為減少,顯著縮短設(shè)計(jì)周期,降低研發(fā)費(fèi)用。
須強(qiáng)調(diào)指出,由于油膜計(jì)算模型本身的局限性,本文只對(duì)部分參數(shù)及計(jì)算數(shù)據(jù)做驗(yàn)證分析,但為實(shí)驗(yàn)的深入延續(xù)提供了較明晰的思路,為后續(xù)探索提供了有力的理論基礎(chǔ)。
上一頁(yè):讀解—巴氏合金的由來(lái)及特性
下一頁(yè):讀解—汽輪機(jī)軸承簡(jiǎn)述